5S Implementation
“A place for everything and everything in its place” is the mantra of the 5S method
5S is a system to reduce waste and optimize productivity through maintaining an orderly workplace and using visual cues to achieve more consistent operational results. The term refers to five steps specified as below
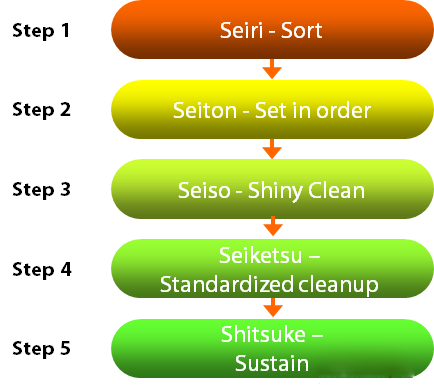
- Seiri - Sorting the Item & streamlining the same.
- Seiton - Remove unnecessary items and disposes them properly.
- Seiso - Keep workplace safe and easy to work.
- Seiketsu - - Standardize the best practices & maintains the same in the work area.
- Shitsuke - keep in working order, Perform regular audits, Training and Discipline.
Implementing the 5S method means cleaning up and organizing the workplace in its existing configuration. It is typically the first lean method that organizations implement. This lean method encourages workers to improve their working conditions and helps them to learn to reduce waste, unplanned downtime, and in-process inventory.
Benefits to the company from using the 5S methodology include raising quality, lowering costs, promoting safety, building customer confidence, increasing factory up-time, and lowering repair costs.
The 5S methodology is typically implemented using a 3-step process, which includes establishing a cross functional team (including employees that work in the associated areas), touring all areas associated with manufacturing process under review, and brainstorming on ways to improve organization to reduce waste.